Industry | Power Generation |
---|---|
Customer | AmerenUE Rush Island Power Plant Jefferson County, Missouri |
Problem
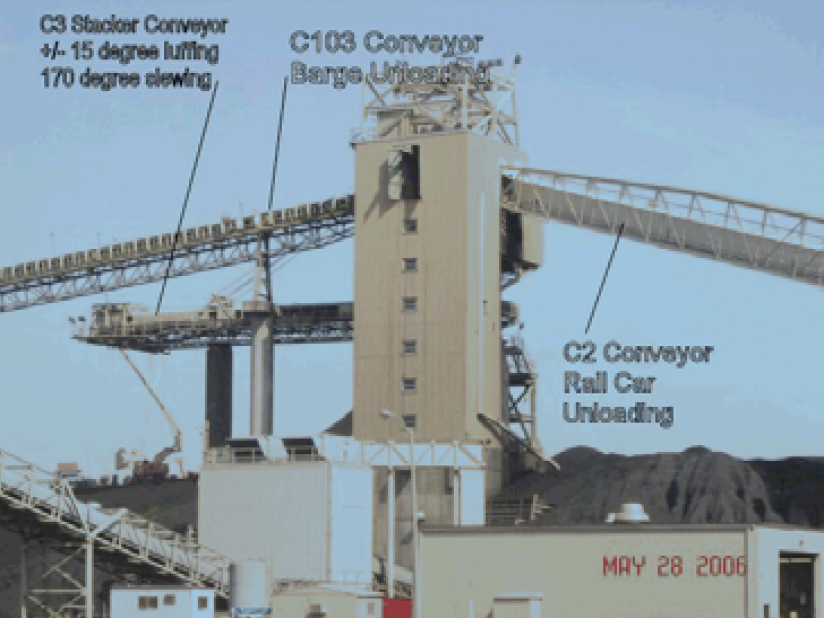
At Rush Island Power Plant, the Stacker Chute transfers coal from the railcar and barge unloading conveyors to the C3 Stacker Conveyor that carries the fuel to the coal yard. All coal burned at the plant–between five and six million tons per year–moves through this chute. The path of Stacker Conveyor C3 is at an angle of roughly 90 degrees from either of the discharging conveyors, making for a difficult transfer. A drop height of 30 feet (9.1 meters) also creates problems, including a large flow of induced air, resulting in dust escape, high levels of impact leading to idler damage and belt abrasion from poor control of the flow of coal onto the receiving belt. Chute capacity also presented a problem. At a flow rate of 4250 tons per hour (3850 mtph), coal backed up inside the chute. This tripped the feed conveyors, producing a bottleneck in coal flow.
Solution
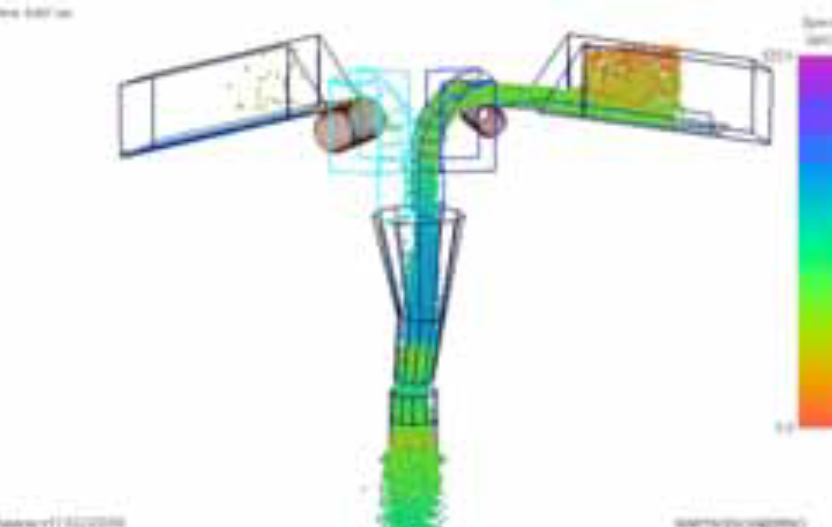
AmerenUE turned to Martin® Transfer Chutes supplied by Martin Engineering. These hood-and-spoon chutes are custom-engineered and computer-modeled in 3D to provide the correct design for the material characteristics and flow rate required. The new engineered flow chutes for Rush Island consisted of two back-to-back hoods. These hoods feed the material into a central chamber that directs the flow down onto a spoon that places the material onto the receiving belt with the proper direction.
Results
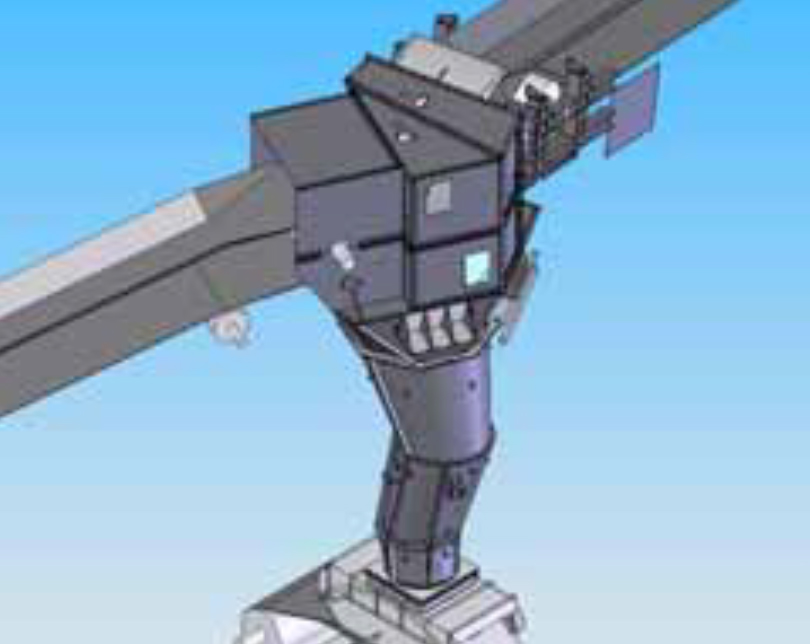
The project was completed in July 2006 on a very tight time schedule; the entire outage time was less than one week. Since the installation, Rush Island Plant operating departments have noticed improvements in coal flow, and improved conveying system reliability with fewer system trips due to plugged chutes. The increased throughput and lack of plugging indicate the problems with coal flow are over. The capacity of the new chutes has beenmeasured at 4300 tph (3900 m/tph) and plant personnel believe that they can handle a much higher rate without blockages. Plant personnel have also noticed a significant reduction in spillage and dust and therefore have been able to reduce cleanup activities.
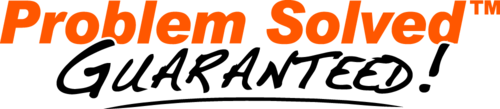
We've solved your problem somewhere before!
While your problem seems unique and frustrating, with 70+ years of solving similar problems around the world, and with the most experienced and educated people on our teams, we can assure you that we’ve “Been There, Done That.” At least close enough to know what needs to be done next and adjust for your situation.
Put Us To The Test For Free! Let Us Give You a Solution.